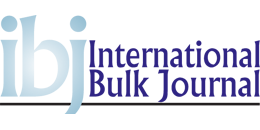

(Posted on 18/04/19)
Hydrex has developed a flexible mobdock repair method that enables the underwater replacement of all types and sizes of shaft seals. This technology has been successfully used by their diver/technicians for over a decade. It allows ship owners to keep their vessel sailing, saving precious time and money.
Damaged stern tube seals will cause an increasing amount of oil leaking or water ingress as the damage worsens. By replacing the seals when the damage is first discovered, Hydrex keeps the down time low. The ship can keep its schedule as seal repairs can be performed during cargo operations. The company does this by creating a dry underwater working environment around the shaft.
It is not always straightforward to replace seals, because there can be quite a bit of variation in the configurations of the stern tube itself. There can also be complications with the liners, which can be worn down and show ruts. All this is routinely handled by Hydrex teams on the jobs.
All shaft seal repairs are performed in cooperation with the OEM. Hydrex usually supplies the equipment but the owner is free to supply his own OEM seals. The teams can handle all type of seals from all manufacturers.
One of the Hydrex diver/technician team carried out underwater stern tube seal repairs on a 225-meter bulk carrier during the vessel’s stop in Ghent. The ship’s stern tube was suffering an oil leak, making a quick on-site repair necessary.
The company’s divers have been using this flexible mobdock technology successfully for almost twenty years and the teams have carried out many underwater shaft seal replacements in that period. As a result the Hydrex technical department was able to offer a repair plan to the customer very quickly.
Once the operation was approved all preparations were handled swiftly. The diver/technicians mobilized to the ship with one of the Hydrex workboats. These are fully equipped as dive support stations.
During the operation the team removed the damaged seals and replaced them with new ones. Working together with the OEM allowed them to provide the customer with original spare parts which guarantees the best quality material. A technician of the seal manufacturer was also present during the operation.
Taking advantage of the Hydrex flexible mobdock technique the team was able to carry out the entire repair on-site and underwater. Because all the required material is ready to be transported at all times, no time is lost making preparations. As a result the owner of the bulk carrier did not have to delay his ship’s schedule unnecessary, let alone arrange a costly and unwelcome trip to drydock.
The Hydrex fast response centers are equipped with all the latest facilities, lightweight equipment and tools. This allows for a timely arrival of teams on any location around the world with everything they need to successfully complete the job.
Pacific Basin Shipping Limited, one of the world’s leading dry bulk shipping companies, has announced... Read more
The shipping industry must accept that geopolitical instability is now a permanent part of the operating... Read more
Algoma Central Corporation has reported its results for the three and six months ended June 30, 2025... Read more
The International Maritime Organization’s Maritime Safety Committee (MSC) has sent a clear message... Read more
Amid increasing pressure on shipping to achieve the IMO 2050 decarbonization targets, the Responsible... Read more
The London P&I Club has renewed calls on ship owners, operators and charterers to address potential... Read more
Columbia Group is calling for urgent reforms in maritime education to address a growing shortage of... Read more
Maritime Information Services (MIS) has officially launched as a global media platform delivering daily... Read more
Russian and Ukrainian seafarers continue to experience significant psychological strain following the... Read more
Noatum Maritime, part of AD Ports Group’s Maritime & Shipping Cluster, announced the official... Read more