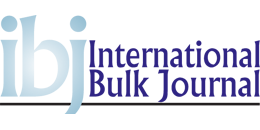

(Posted on 14/04/22)
A report by the University of Queensland and the University of Geneva indicates that sand from iron ore production can reduce carbon emissions
The University of Queensland (UQ), through its Sustainable Minerals Institute (SMI), and the University of Geneva (UNIGE) has released a report indicating that sand from the ore production process may contribute to solve two important environmental issues by reducing sand extracted from the natural environment and the mining tailings generation. Vale contributed to the report and facilitated the sampling of its Sustainable Sand produced at the Brucutu mine (MG) for an independent analysis.
Vale’s Sustainable Sand is a co-product of iron ore processing. Based on adjustments in the operation, the sandy material, previously disposed in piles and dams, is now processed and transformed into a product, following the same quality controls as in the iron ore production. This year, Vale will allocate around 1 million tons of sand, between sales and donations, for use in civil construction and tests in pavement, among other uses.
The report carried out by the universities, called “Ore-sand: A potential new solution to the mining tailings and global sand sustainability crises”, investigated whether sand from ore processing, described by the term “ore-sand”, could become a sustainable source of sand and at the same time reduce the volume of tailings generated by mining.
Material characterisation results from the report indicate that the sampled material is inert and non-toxic, and can be suitable for certain applications, either on its own or as a part of a blend, such as with coarser sand, in order to meet specific grading requirements. Separating and repurposing these sand-like materials before they are added to the waste stream would not only significantly reduce the volume of waste being generated but could also create a responsible source of sand.
The report found that, from a technical perspective, sand from iron ore operations can be a direct substitute for sand extracted from the environment in brick making, pavement, in embankments, and cement manufacturing. When mixed with coarser sand and other aggregates, it can be used in the production of concrete and mortar, drainage and soil improvement, and water treatment.
The life cycle assessment of “ore-sand”, based on the case of Vale's Sustainable Sand, also shows that this material has the potential to present lower net carbon emissions during its production when compared to sand extracted from the environment. However, to get a better idea of the potential of this reduction, it is necessary to carry out an assessment of the product's transport stage, which was not covered in this report.
The partnership between Vale and the universities was born in an event held in 2018 at the Brazilian company’s office in Switzerland, where Vale’s engineer Emile Scheepers presented his research on applications for sandy material for the production of quartz surfaces used in, for example, kitchen countertops. This project began in 2013 and was followed by other research initiatives in Brazil aiming at the reduction of tailings in iron ore production.
“Vale has already invested around R$ 50 million and has partnered with more than 40 organizations, including universities, research centers and national and foreign companies, to study applications for material from iron ore processing,” explains André Vilhena, manager of New Businesses at Vale. “Our aim is to innovate to make mining more sustainable and smart, promoting the circular economy and benefiting society.”
In 2021, Vale started selling Sustainable Sand, a co-product from iron ore processing. About 250,000 tons of sand were processed and destined for sale or donation for use in concrete, mortar, prefabricated materials, artifacts, cement and road paving. Each ton of sand produced represents one ton less of tailings being disposed of in piles or dams.
Metso has completed the expansion of its service centre in Antofagasta, Chile, reinforcing its ability... Read more
Alcoa of Australia Limited, a wholly-owned subsidiary of Alcoa Corporation has announced a Joint Development... Read more
Rio Tinto has published detailed information on its global tailings facilities, in alignment with the... Read more
The National Grain and Feed Association (NGFA) has commended the U.S. Senate for confirming Luke... Read more
Cargill, one of the world’s leading food providers, continues to advance its growth strategy in... Read more
Rio Tinto has announced a 6% production year-on-year uplift, thereby delivering on strategy through... Read more
The Korea Trade Insurance Corporation (K-SURE) and Trafigura, a global leader in the commodities industry... Read more
BHP have released their Operational Review for the year ended 30 June 2025.BHP Chief Executive Officer... Read more
A strategic collaboration between Icon Gulf Trading DMCC (part of the Dynamic Group) and GeoServe Energy... Read more
SSAB and Metal Solutions have entered a long-term partnership for the supply of decarbonized steel with... Read more