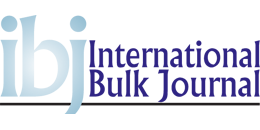

(Posted on 12/10/20)
As part of its environmental modernization program, by 2024 RUSAL, a leading global aluminium producer, plans to completely switch the reduction area of the Krasnoyarsk aluminium smelter (KrAZ) to a new type of raw material, an eco-friendly pitch.
In 2019, RUSAL accounted for about 5.9% of global production of aluminium and 6.3% of alumina production. RUSAL's offices are operating in 20 countries all over the world and across 5 continents.
Unlike the traditional raw material, eco-friendly pitch is less tarry in nature and its application in the aluminium production process is less harmful for the environment. The implementation of this and other technical innovations at KrAZ will lead to a reduction of benzapyrene emissions’ by at least 60% in the upcoming years.
“The transition to the eco – friendly pitch at a production facility is a complex technological process. The environmental efficiency from using the material is confirmed by laboratory tests conducted by the RUSAL’s engineering and technology center (ETC). We are glad to see that RUSAL has been initiating and implementing the most favourable environmental solutions at KrAZ for more than 15 years whilst also interacting with authorities and the locals”, said Vitaly Badmaev, first Deputy Minister of ecology and environmental management of the Krasnoyarsk territory.
“The transition to a new eco – friendly type of raw material developed by the RUSAL engineering center at the Krasnoyarsk aluminum smelter is not a simple process; it is very dependent on suppliers who must modernize their own production. We also continue to invest in R&D and work with suppliers who could produce both this and other types of eco - friendly raw materials for us in the required volume, because environmental issues are an absolute priority today." said Viktor Mann, RUSAL's technical Director.
The comprehensive environmental program at KrAZ was launched in 2004 and comprised two stages. The first stage focused on the smelter building and involved commissioning new gas treatment systems, installing an automated production process management system, and introducing the dry anode process. The second stage involved introducing the best available technologies including the modification of KrAZ reduction cells to utilise the EcoSoderberg process.
As a result of the 16-year environmental program, the smelter's total emissions have been cut by 38%, while fluoride emissions are down by 76%. Today, the smelter's emissions, which end up in the air of the city, are 4.5 times less than they were back in 1980.
Metso has completed the expansion of its service centre in Antofagasta, Chile, reinforcing its ability... Read more
Alcoa of Australia Limited, a wholly-owned subsidiary of Alcoa Corporation has announced a Joint Development... Read more
Rio Tinto has published detailed information on its global tailings facilities, in alignment with the... Read more
The National Grain and Feed Association (NGFA) has commended the U.S. Senate for confirming Luke... Read more
Cargill, one of the world’s leading food providers, continues to advance its growth strategy in... Read more
Rio Tinto has announced a 6% production year-on-year uplift, thereby delivering on strategy through... Read more
The Korea Trade Insurance Corporation (K-SURE) and Trafigura, a global leader in the commodities industry... Read more
BHP have released their Operational Review for the year ended 30 June 2025.BHP Chief Executive Officer... Read more
A strategic collaboration between Icon Gulf Trading DMCC (part of the Dynamic Group) and GeoServe Energy... Read more
SSAB and Metal Solutions have entered a long-term partnership for the supply of decarbonized steel with... Read more