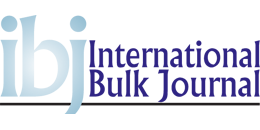

(Posted on 03/10/19)
Rudders, thrusters, nozzles and other underwater running gear are exceptionally prone to corrosion and cavitation damage. Cavitation is caused by the spinning of propeller blades. If running gear is not given the proper protection against this the damage can be severe.
This leads to expensive and time-consuming repairs in drydock at the least or malfunctioning of the running gear at worst. A rudder has been found missing in its entirety on more than a few occasions, unfortunately. This will have substantial financial consequences for a shipowner.
Applying Ecoshield is a fast and easy to learn process. As a result an application is very flexible and can easily be scheduled around the planning of the yard. Only two layers are required. The minimum overcoating time between these layers is only three hours. This means that most running gear can be coated in a single day.
Newbuild ships benefit the most from Ecoshield. Applying the coating during building means a vessel’s running gear will be protected from the moment the ship leaves the shipyard until the end of its service life. A shipowner will not have to worry about repainting during any of the scheduled dockings.
An existing ship can also be protected with Ecoshield. If for instance a rudder has already suffered corrosion damage, the coating can prevent any further damage from occurring. In such case Ecoshield can be used in combination with another product in the Subsea Industries family: Ecofix.
Ecofix is a superior, tested and proven filler that restores the steel to its original shape with a smooth surface prior to recoating. Because it uses the same basic resin, Ecoshield can be applied just one hour after the filler.
Hundreds of successful Ecoshield applications have been carried out over the last years. Just in the last few weeks several rudders, thruster tunnels and nozzles were coated with Ecoshield. These applications were performed on different types of vessels in shipyards across the globe.
Shipowners that started with a single rudder as a test have since then ordered the same protection for the running gear of their entire fleet. Several have included the coating in the newbuild specs to make sure cavitation and corrosion can not touch the steel of their ship’s running gear. Even after years of service these owners are experiencing zero cavitation damage and failure.
Strategic lifting capacity meets India’s east coast logistics growth. The LHM 550s selected for... Read more
A new advanced simulation suite supplied by technology group Wärtsilä for the Akademi Laut... Read more
The New Nuclear for Maritime European Summit, the world’s largest international summit on maritime... Read more
Steelpaint GmbH has received its first order from Singapore-based Winning International Group to supply... Read more
Anemoi Marine Technologies, a leader in wind-assisted propulsion technology, has developed an in-service... Read more
A new recruitment feature has launched to help dismantle the shadow network of rogue crewing agents... Read more
AUMUND has announced that, as of 25 June, 2025, ESI Eurosilo B.V., headquartered in Purmerend, the Netherlands... Read more
Anemoi Marine Technologies, a global leader in wind propulsion solutions, has announced the official... Read more
Data alone doesn’t solve problems. It is the ability to propel data into transformative action... Read more
Turkish shipowner, Susesea, has successfully upgraded the cylinder lubrication strategy across its fleet... Read more