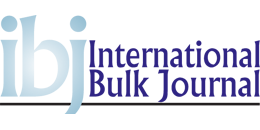

(Posted on 01/07/21)
The decision to apply the award-winning Ecoshield hard coating to rudders and thrusters is paying dividends, with a number of shipowners noticing zero cavitation damage and failure compared to equipment coated with other protective systems.
Some of them were new customers, some returning ones. They had experienced firsthand the devastating effect of cavitation when a traditional coating system is used. For this reason they decided to use Ecoshield to ensure lasting protection against corrosion and erosion damage for the rudders, nozzle rings and tunnel thrusters of their vessels.
Ecoshield has been designed to give a very thorough and lasting protection against cavitation and corrosion. If the cavitation cannot pierce the coating then no other damage can occur.
Tests conducted in a flow channel have confirmed that Ecoshield performs extremely well under severe cavitation. These tests were divided into six stages during which the coating was exposed to an increasing pressure drop, creating a growing cavitation force. Even after the last stage no erosion was present on the patch coated with Ecospeed.
Besides offering rudder protection Ecoshield is also suitable for thrusters, azimuth thrusters, azipods, thruster nozzles, thruster tunnels and other underwater ship gear which needs special protection from corrosion. The extra strength coating protects these areas for the service life of the ship. There is no need for recoating or major repair.
Protection of the running gear of your vessel is best begun at the newbuild phase. When a vessel comes into drydock, maintenance of its stern area, especially cavitation damage repair, can take a long time. There are strict procedures concerning blasting, painting, welding and propeller and stern tube seal work. Painting is then assigned to the end of the schedule. As a consequence it may be rushed or not done at all or else prolong the stay in drydock.
With an Ecoshield application one can avoid these problems from day one because no repaint of the running gear will be needed during drydocking. Ecoshield will remain intact for the lifetime of the vessel and is guaranteed for ten years. At the most, touch-ups amounting to less than 1% of the surface area will be required. Planning the maintenance of the vessel’s stern area therefore becomes much easier.
The newbuild phase is the perfect time to apply Ecoshield. However, the coating can also be used to protect vessels that have been in service for some time and are already facing cavitation and corrosion damage.
Ecoshield’s flexibility makes it easy to adapt the application schedule to the rest of the activities at the shipyard or drydock in a way which does not interfere with them. Overcoating time can be as short as three hours. This means that for smaller surfaces such as rudders or bow thrusters the two required coats can usually be applied in one single day.
Strategic lifting capacity meets India’s east coast logistics growth. The LHM 550s selected for... Read more
A new advanced simulation suite supplied by technology group Wärtsilä for the Akademi Laut... Read more
The New Nuclear for Maritime European Summit, the world’s largest international summit on maritime... Read more
Steelpaint GmbH has received its first order from Singapore-based Winning International Group to supply... Read more
Anemoi Marine Technologies, a leader in wind-assisted propulsion technology, has developed an in-service... Read more
A new recruitment feature has launched to help dismantle the shadow network of rogue crewing agents... Read more
AUMUND has announced that, as of 25 June, 2025, ESI Eurosilo B.V., headquartered in Purmerend, the Netherlands... Read more
Anemoi Marine Technologies, a global leader in wind propulsion solutions, has announced the official... Read more
Data alone doesn’t solve problems. It is the ability to propel data into transformative action... Read more
Turkish shipowner, Susesea, has successfully upgraded the cylinder lubrication strategy across its fleet... Read more