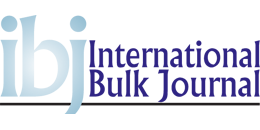

(Posted on 23/11/20)
Bühler is heralding a new age in milling technology with the launch of Arrius, a fully integrated grinding technology for milling wheat, durum, rye, barley, corn, and spelt.
The launch follows a fundamental rethink of the traditional grinding methods that lie at the heart of the milling process. By redesigning each technology component, Bühler has produced an integrated and self-adjusting grinding system that is a radical step change in how millers are able to control the quality and consistency of their product. Other benefits include cutting energy costs, increasing staff safety, speedy installation, remote digital control, improved food safety, and reducing the initial outlay needed for plant investment.
These advancements come as the milling industry faces a number of commercial challenges with clients demanding ever-increasing consistency and higher product quality. In a highly price-sensitive and competitive market even the smallest deviation in production parameters goes straight to a miller’s bottom line. This is happening as food safety regulations tighten and millers report difficulty finding properly qualified and skilled staff.
Addressing these challenges will require ever-greater automation. Arrius is set to play a key role as the milling industry evolves towards autonomous mills capable of self-adjusting to optimize production parameters.
At the heart of the Arrius step change lie the sensors in the feeding module and the roller pack enabling greater control of the product flow and grinding process. It means Arrius is able to automatically adjust to the characteristics of the raw material. Double-sided sensors in the robust new roller pack allow millers, for the first time, to continuously measure the grinding force of the rollers. This unique feature allows the miller to control the grinding process closely and thus optimize product characteristics for their specific market.
Besides the particle size distribution, starch damage is a parameter that can be influenced as precisely as never before. With Arrius it is possible to better control the grinding process of the product and increase starch damage by up to 10% if required.
Energy is a significant cost driver for millers, so Arrius has also been designed with an integrated drive and gearbox, resulting in energy cost savings of up to 10%.
Arrius’s new ease-of-use features includes a remote app that can be loaded on smartphones or tablets from which an operator can control all grinding parameters from anywhere within the mill’s network.
New food safety features include a feeding module designed for total product discharge. A streamlined design and increased aspiration in the grinding chamber also cut product deposits. The hygienic levelling feet that support the machinery are designed to improve food safety by enabling total under-machine cleaning. An electronically lockable cover and hand guard protection provides a new benchmark in operational safety to protect staff.
Thanks to the integrated drive and switch cabinet Arrius can be flexibly positioned in the mill and quickly installed. Arrius can reduce the cost of building investment as it makes a complete floor obsolete. Thanks to the integration of components and reducing the number of power and data cables from around 10 to only three, Arrius can be installed in a third of the time.
Metso has completed the expansion of its service centre in Antofagasta, Chile, reinforcing its ability... Read more
Alcoa of Australia Limited, a wholly-owned subsidiary of Alcoa Corporation has announced a Joint Development... Read more
Rio Tinto has published detailed information on its global tailings facilities, in alignment with the... Read more
The National Grain and Feed Association (NGFA) has commended the U.S. Senate for confirming Luke... Read more
Cargill, one of the world’s leading food providers, continues to advance its growth strategy in... Read more
Rio Tinto has announced a 6% production year-on-year uplift, thereby delivering on strategy through... Read more
The Korea Trade Insurance Corporation (K-SURE) and Trafigura, a global leader in the commodities industry... Read more
BHP have released their Operational Review for the year ended 30 June 2025.BHP Chief Executive Officer... Read more
A strategic collaboration between Icon Gulf Trading DMCC (part of the Dynamic Group) and GeoServe Energy... Read more
SSAB and Metal Solutions have entered a long-term partnership for the supply of decarbonized steel with... Read more