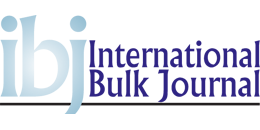

(Posted on 28/08/18)
An innovative cement manufacturer in the Midwestern U.S. has implemented a unique power solution at a remote conveyor location that lacked convenient electrical access. The patent-pending design uses the kinetic energy of the moving belt to generate enough electricity to drive an automated dust suppression system, a pneumatic belt cleaner tensioner and a series of air cannons, helping operators at the Illinois Cement Plant reduce fugitive dust and spillage, increase cargo flow efficiency and minimize labor costs for cleaning and maintenance.
The Martin Roll Gen System is designed to create a self-contained mini power station that allows operators to run electrical monitoring systems, safety devices and a variety of other components. Able to be retrofitted on existing idler support structures, the generator can be employed on virtually any steel roller. The device is considered a significant step toward eliminating power production obstacles, as conveyors move into the next generation of “smart systems” that are predicted to be more sustainable and autonomous.
“Running auxiliary power can be both complicated and costly, requiring expensive labor and oversized cables to accommodate the inevitable voltage drop over long runs, as well as transformers, conduit, junction boxes and other components,” commented Andrew Timmerman, Product Development Engineer at Martin Engineering. “And using even a small conventional generator to provide power introduces a different set of issues, including flammable fuels.”
Conveyor #107-1 is the longest outdoor conveyor system on the Illinois Cement site, running 600 feet (182 m) and discharging either onto the #107-2 stack-out conveyor or the 250-foot-long (75 meter) belt leading directly into the plant, based upon immediate production needs. It’s a 30-inch wide (762 mm) mechanically-spliced belt with a 35º trough that travels at ~400 fpm (2 mps), conveying nearly 300 st/h (272 mt/h) of limestone.
Material arriving from the quarry can be either wet, dry and dusty or anything in between, depending on the season and weather. The changing work environment presented challenges throughout the entire conveying system, with different weather conditions triggering various types of carryback. Cleanup was labor-intensive.
Phase one of the Martin Engineering solution involved placing a “smart” dust suppression system at the transfer point between the 153 and 107-1 conveyors. Phase two included an automated, pneumatically-tensioned belt cleaner and air cannon system at 107-1’s discharge zone. Both components are powered by the Roll Gen System.
To manage the dust, technicians installed a Martin Surfactant Dust System at the transfer point between 153 and 170-1 to deliver a chemically-enhanced water spray as a topical treatment for material at the point of emission. Triggered by a sensor as soon as the load enters the transfer point, the system supports dust mitigation measures already in place to minimize the labor needed for maintenance and replacement of the dust collector cartridges.
The use of multiple technologies working in tandem to control material flow and prevent fugitive particles has dramatically improved the material handling system’s efficiency. The modifications have helped Illinois Cement reduce labor and equipment expenses, considerably cutting the manpower needed to clean spillage along the conveyor path. The result is a cleaner, safer and more productive operation.
Strategic lifting capacity meets India’s east coast logistics growth. The LHM 550s selected for... Read more
A new advanced simulation suite supplied by technology group Wärtsilä for the Akademi Laut... Read more
The New Nuclear for Maritime European Summit, the world’s largest international summit on maritime... Read more
Steelpaint GmbH has received its first order from Singapore-based Winning International Group to supply... Read more
Anemoi Marine Technologies, a leader in wind-assisted propulsion technology, has developed an in-service... Read more
A new recruitment feature has launched to help dismantle the shadow network of rogue crewing agents... Read more
AUMUND has announced that, as of 25 June, 2025, ESI Eurosilo B.V., headquartered in Purmerend, the Netherlands... Read more
Anemoi Marine Technologies, a global leader in wind propulsion solutions, has announced the official... Read more
Data alone doesn’t solve problems. It is the ability to propel data into transformative action... Read more
Turkish shipowner, Susesea, has successfully upgraded the cylinder lubrication strategy across its fleet... Read more