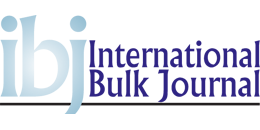

(Posted on 14/06/24)
Future newbuild ships of all types should be built without a sterntube and with a seawater-lubricated propeller shaft bearing arrangement, according to Blue Ocean Alliance’s Chris Leontopoulos.
Speaking at a recent maritime industry forum in Hamburg, Mr. Leontopoulos said the sterntubeless ship design – jointly developed by Blue Ocean Alliance members ABS, Thordon Bearings, Shanghai Merchant Ship Design and Research Institute (SDARI), Wärtsilä, and the National Technical University of Athens (NTUA) – is so commercially, operationally and environmentally attractive that “I personally hope that in the future all ships are built like this”.
Kick-starting his presentation with the startling statistic that more than eight million litres of sterntube lubricating oil is polluting the oceans annually, Mr. Leontopoulos, ABS’ Vice President, Technology, EMEA, said the design interventions proposed by the group can deliver a commercially and environmentally optimal vessel capable of saving hundreds of thousands of dollars in operational costs. This, without changing hull lines or existing class rules and regulations.
“We decided to remove the sterntube, and by shortening propeller shaft length and moving the prime mover further aft, we no longer needed a forward sterntube bearing. This places less friction on the shaft, resulting in lower power loss, improved fuel efficiency and reduced emissions. A sterntubeless ship also results in a bigger cargo space for the same vessel length,” he said.
Mr. Leontopoulos went on to say that the use of a seawater-lubricated bearing with a tapered key design – the principal component that makes the sterntubeless ship possible – also removes the need for an aft seal and a shaft coating system. The sterntubeless design features a seawater-lubricated bearing, a Wärtsilä forward shaft seal, a Water Quality Package and a bulkhead seal.
The technical differences were immediately obvious when a graphic was shown comparing a ship with and without a sterntube.
Essentially, the design presents a dry internal inspection chamber aft of the engine room, in the space normally given to the sterntube. This new space, big enough for engineers to stand up in to maintain or replace propeller shaft components while the ship is afloat, has been created by trimming stiffeners and cutting an opening into the bulkhead.
“This is a very a big advantage because you don’t have to drydock the ship and withdraw the shaft or propeller to monitor and maintain seawater-lubricated bearings and seals. We can now do this from inside the ship while the vessel is operational,” said Mr. Leontopoulos.
The sterntubeless ship, he said, also negates the need to realign the shaft throughout the vessel’s lifetime, mitigating the risk of shaft damage or indentation, which can result in substantial downtime and expenditure.
Going on to reveal the cost benefits of a sterntubeless ship, Mr. Leontopoulos acknowledged that although the estimated CAPEX for additional components could add about US$10,000 to $30,000 to the cost of a newbuild depending on shaft diameter, the ROI is quick given the reduced operational expenditure. This is where the real financial gain is to be made.
He told conference delegates that aside from immediate savings of US$350,000 in lubricating oil, operators could save more than US$1 million in through-life operational costs.
This is based on reduced fuel consumption, reduced drydocking and maintenance costs, and associated loss of earnings; shaft alignment optimization, lower bearing wear rates, better EEDI; and an increase in cargo carrying capacity. The arrangement also reduces to zero the risk of environmental fines related to sterntube oil pollution.
Summing up he said: “There's no pollution risk, no oil changes, and no need to drydock to change the bearing. A shorter shaft line and smaller engine room space increases cargo space and improves EEDI ratings; there is no barred speed range and no fatigue concerns. It complies completely with all existing class rules.”
Strategic lifting capacity meets India’s east coast logistics growth. The LHM 550s selected for... Read more
A new advanced simulation suite supplied by technology group Wärtsilä for the Akademi Laut... Read more
The New Nuclear for Maritime European Summit, the world’s largest international summit on maritime... Read more
Steelpaint GmbH has received its first order from Singapore-based Winning International Group to supply... Read more
Anemoi Marine Technologies, a leader in wind-assisted propulsion technology, has developed an in-service... Read more
A new recruitment feature has launched to help dismantle the shadow network of rogue crewing agents... Read more
AUMUND has announced that, as of 25 June, 2025, ESI Eurosilo B.V., headquartered in Purmerend, the Netherlands... Read more
Anemoi Marine Technologies, a global leader in wind propulsion solutions, has announced the official... Read more
Data alone doesn’t solve problems. It is the ability to propel data into transformative action... Read more
Turkish shipowner, Susesea, has successfully upgraded the cylinder lubrication strategy across its fleet... Read more