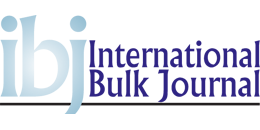

(Posted on 24/05/18)
A global leader in conveyor technology has helped mitigate dust emissions at the underground limestone mine of a cement production plant by implementing an innovative transfer point solution. Using a specially-designed dust control unit (DCU) to spray a surfactant onto both sides of the cargo stream during transfer onto the main conveyor, Martin Engineering was able to help Continental Cement Company, LLC, suppress fugitive dust both along the underground belt path and during discharge at the outdoor storage yard. The result was a significant reduction in dust emissions, creating a safer workplace and offering a measurable return on investment.
Continental Cement has been in operation since 1903. Over more than a century, the company has continued to improve and increase operations to reach a current cement production capacity of 1.2 million short tons (≈1.1 mil. tonnes) of clinker annually.
A 350 foot (106 m) underground mine now provides the primary source of limestone, which makes up 75% of the raw material required to produce the meal in the company’s Type I/II, and Type III Portland cement. Yielding 1.6 million short tons (≈1.4 million tonnes) of limestone annually, the extracted material is transported via truck and high-speed conveyors in order to move it to the surface, where it is held in a 100,000 ton (≈91,000 tonne) outdoor storage pile, then processed through a four-stage preheater/precalciner dry process cement kiln.
Fifty-ton trucks dump 600-650 t/h (544-589 mt/h) of extracted limestone into an underground hopper that feeds an impact crusher, which reduces the rocks to 4-in. (101 mm) minus. The aggregate is then loaded onto Conveyor 0, a 60-inch (1524 mm) wide belt traveling approximately 700 fpm (3.5 m/s) for 400 feet (122 m). The rock is discharged through a transfer chute onto Conveyor 1, travelling up the 1,300 foot (400 m) inclined belt to the surface and dropping 20 feet (6 m) onto the outdoor storage pile.
“The two main areas we identified as having unacceptable dust emissions were at the underground crusher hopper and outdoors where the material was discharged onto the stockpile,” explained Environmental Manager Leonard Rosenkrans.
The original dust control equipment followed a traditional approach, with a goal of wetting the surface of the cargo. However, operators learned that limestone dust was not being adequately controlled by the water alone. Martin Engineering representatives visited the site with a trailer containing a fully functional Martin® Dust Control Unit (DCU), allowing a full demonstration of the unit’s capabilities. Conducting an end-to-end walkthrough of the cargo flow, technicians were able to determine the best course of action.
Grupo Servicios Marítimos (GSM), in partnership with Neuero, has delivered a groundbreaking solution... Read more
Elcome International’s WELCOME Maritime Wi-Fi, now marking one year of service, has emerged as... Read more
Amid increasing pressure on shipping to achieve the IMO 2050 decarbonisation targets, the Responsible... Read more
MacGregor continues to serve its maritime and offshore customers with its wide portfolio of cargo and... Read more
The board of directors of MacGregor Group AB has appointed Jonas Gustavsson Chief Executive Officer... Read more
Strategic lifting capacity meets India’s east coast logistics growth. The LHM 550s selected for... Read more
A new advanced simulation suite supplied by technology group Wärtsilä for the Akademi Laut... Read more
The New Nuclear for Maritime European Summit, the world’s largest international summit on maritime... Read more
Steelpaint GmbH has received its first order from Singapore-based Winning International Group to supply... Read more
Anemoi Marine Technologies, a leader in wind-assisted propulsion technology, has developed an in-service... Read more