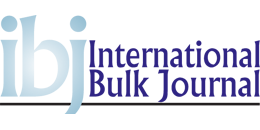

(Posted on 22/05/20)
The final vessel in a series of five ship-assist tugs has been successfully converted to Thordon’s RiverTough tailshaft bearings and TG100 shaft seals and has returned to work on the Mississippi River.
These five tugs are considered to be the first ship-assist tugs operating in the lower Mississippi fitted with both RiverTough bearings and TG100 seals.
The New-Orleans-based tug operator converted its first vessel – a 117ft (35m), 4200hp twin-screw ship-assist tug – in 2015 to reduce the operating and maintenance costs associated with traditional rubber tailshaft bearings and clad welded journals.
According to Thordon Bearings’ Sales Manager, Jim Bright, who was involved in all five retrofits, the owner specified the solution because it was tired of unbudgeted costs following frequent premature bearing and shaft wear. The owner was familiar with the reputation of RiverTough bearings and its performance on other workboats.
“Their previous arrangements of rubber bearings had to be replaced every two years or so and the shafts needed to be repaired due to excessive wear. This can be avoided with Thordon’s products,” said Bright.
When RiverTough bearings are used by workboats, they routinely provide wear rates of 0.003" to 0.004" (0.075mm to 0.100mm) in 6000 to 7000 hours of annual use on the Mississippi River.
This upgrade was the first ship-assist tug in the New Orleans Port to change over to Thordon.
"We proposed retrofitting the RiverTough tailshaft bearing in conjunction with a ThorSleeve hardened shaft sleeve, and a TG100 shaft seal. This is a much more suitable shafting solution for vessels operating in abrasive rivers like the Mississippi,” Bright stated.
However, during discussions with the owner it emerged that a different installation method was required.
The traditional approach of casting Chockfast (an epoxy resin) directly to the outside diameter of the bearing meant that the Chockfast resin had to be chiseled out each time the existing rubber bearing needed replacing.
A new rubber bearing would have to be installed every 18-24 months. The bearing would have to be aligned and new Chockfast cast around them. This added to the time that the vessel was docked for repairs which in turn meant additional costs. When you factor the lost charter work into the equation, this process can be very costly for the ship owner.
Thordon’s solution was to create a permanent housing using the Chockfast epoxy grout.
Grupo Servicios Marítimos (GSM), in partnership with Neuero, has delivered a groundbreaking solution... Read more
Elcome International’s WELCOME Maritime Wi-Fi, now marking one year of service, has emerged as... Read more
Amid increasing pressure on shipping to achieve the IMO 2050 decarbonisation targets, the Responsible... Read more
MacGregor continues to serve its maritime and offshore customers with its wide portfolio of cargo and... Read more
The board of directors of MacGregor Group AB has appointed Jonas Gustavsson Chief Executive Officer... Read more
Strategic lifting capacity meets India’s east coast logistics growth. The LHM 550s selected for... Read more
A new advanced simulation suite supplied by technology group Wärtsilä for the Akademi Laut... Read more
The New Nuclear for Maritime European Summit, the world’s largest international summit on maritime... Read more
Steelpaint GmbH has received its first order from Singapore-based Winning International Group to supply... Read more
Anemoi Marine Technologies, a leader in wind-assisted propulsion technology, has developed an in-service... Read more