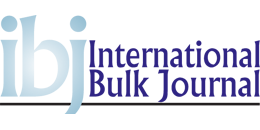

(Posted on 20/12/19)
A new conveyor belt cleaner has been designed with an innovative method of holding the urethane blade in place without the need to mill any slots for holding pins. Combining the benefits of previous designs into one product, the QC1+TM Belt Cleaner from Martin Engineering can be cut to length to fit virtually any application, reducing the need for customers to stock multiple blade sizes to accommodate different belt widths. Operators simply trim the blade to the desired size from the stock 9-foot (2.74 meter) length to match the material path, slide in the blade holders and lock them in position. The new blade can be retrofitted to virtually any Martin main frame and most competing designs.
“In most belt cleaner designs, the blade is pinned in place, but this new approach uses a hole right in the aluminum extrusion to keep the blade firmly in position,” explained Conveyor Products Manager Dave Mueller. “The biggest benefit to customers is the ability to buy long length blades and cut them to size without doing any machining. Most customers have a number of different belt widths, so in the past they’ve had to stock different blade sizes. But this design can accommodate a wide range of belts with a single product.”
In some applications, existing cleaner designs are limited by the placement of the pin holes. In the case of a 36” (91.4 cm) wide belt that has a material path of just 20″ (51 cm), for example, there might be pin holes at 2″ (5 cm), 6″ (15 cm) and 8″ (20.3 cm), with no holes for a 20″ blade. The result would be the dreaded ‘smiley face’ wear pattern, and the uneven blade wear shortened its service life.
“With this design, the blade holders slide and lock on a blade guide rail, and are adjustable to whatever width is needed to match the material path,” Mueller said. “That contributes to better cleaning efficiency and longer blade life.”
The mainframes on the QC1+ are 3-piece assemblies, with a square center section and a torque tube sliding into each end. The tubes are formed from high-strength steel and engage in the corners of the square main frame. They transmit the torque from the tensioner through the tubes and into the main frame to maintain blade tension.
The torque tube lock collars are designed to be an interference fit with the square mainframe. To assemble, the tube is installed first, then the collars are added and set in position. The length of the mainframe is adjusted next, and finally the set screws on the collars are tightened down. In most applications, the simple sequence can be performed by a single worker in just a few minutes. The new design is compatible with any of the Martin tensioning systems.
Urethane belt cleaner blades from Martin Engineering are designed with the company’s patented Constant-Area Radial Pressure (CARP) technology to deliver consistent cleaning throughout all stages of blade life. Martin designed and developed the concept, patented in 1990, which has been adopted worldwide. The innovative cleaners maintain the same contact area, blade angle and pressure to effectively remove virtually any type of material carryback, even as the blade wears down over time.
Martin Engineering has been a global innovator in the bulk material handling industry for 75 years, developing new solutions to common problems and participating in industry organizations to improve safety and productivity.
Grupo Servicios Marítimos (GSM), in partnership with Neuero, has delivered a groundbreaking solution... Read more
Elcome International’s WELCOME Maritime Wi-Fi, now marking one year of service, has emerged as... Read more
Amid increasing pressure on shipping to achieve the IMO 2050 decarbonisation targets, the Responsible... Read more
MacGregor continues to serve its maritime and offshore customers with its wide portfolio of cargo and... Read more
The board of directors of MacGregor Group AB has appointed Jonas Gustavsson Chief Executive Officer... Read more
Strategic lifting capacity meets India’s east coast logistics growth. The LHM 550s selected for... Read more
A new advanced simulation suite supplied by technology group Wärtsilä for the Akademi Laut... Read more
The New Nuclear for Maritime European Summit, the world’s largest international summit on maritime... Read more
Steelpaint GmbH has received its first order from Singapore-based Winning International Group to supply... Read more
Anemoi Marine Technologies, a leader in wind-assisted propulsion technology, has developed an in-service... Read more