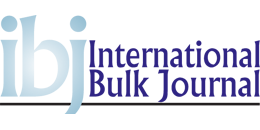

(Posted on 12/02/19)
In the past year numerous rudders, thruster tunnels and nozzles were coated with the Ecoshield protective coating system designed specifically to give lasting protection against cavitation and corrosion damage.
In 2018 applications were carried out in shipyards in Turkey, the Netherlands, Singapore, Hong Kong, China, Japan, Denmark, Estonia, Germany and the United States and this on a wide range of ships. These included vehicle carriers, ferries, tankers, yachts, research vessels and container ships. The rudders as well as the running gear of these ships will be protected against cavitation and corrosion damage for the rest of their service lives.
Well over thirty vessels belonging to fourteen different owners were treated. Some of them were new Subsea Industries customers, some returning ones. They had experienced firsthand the devastating effect of cavitation when a traditional coating system is used. For this reason they decided to use Ecoshield to ensure lasting protection against corrosion and erosion damage for the rudders, nozzle rings and tunnel thrusters of their vessels.
Ecoshield has been designed to give a very thorough and lasting protection against cavitation and corrosion. If the cavitation cannot pierce the coating then no other damage can occur.
Tests conducted in a flow channel have confirmed that Ecoshield performs extremely well under severe cavitation. These tests were divided into six stages during which the coating was exposed to an increasing pressure drop, creating a growing cavitation force. Even after the last stage no erosion was present on the patch coated with Ecospeed.
Understandably the owner then wants to try to hold off going to drydock as long as possible and ideally until the five year interval has passed. Temporary repairs are carried out after which the class requires that a new inspection is performed every three months.
When such a vessel eventually comes into drydock, maintenance work on the vessel’s stern area, especially cavitation damage repair, can take a long time. Most of these repairs cannot be performed concurrently. This is the result of the close proximity of the rudder, the propeller and the stern area, along with the strict procedures concerning blasting, painting and welding work. Painting is therefore usually assigned to the end of the schedule and as a consequence may not get done at all or else prolongs the stay in drydock. Taking into account the tight drydock schedule of most vessels this is often very problematic.
The newbuild phase is the perfect time to apply Ecoshield. However, the coating can also be used to protect vessels that have been in service for some time and are already facing cavitation and corrosion damage.
Ecoshield’s flexibility makes it easy to adapt the application schedule to the rest of the activities at the shipyard or drydock in a way which does not interfere with them. Overcoating time can be as short as three hours. This means that for smaller surfaces such as rudders or bow thrusters the two required coats can usually be applied in one single day.
Grupo Servicios Marítimos (GSM), in partnership with Neuero, has delivered a groundbreaking solution... Read more
Elcome International’s WELCOME Maritime Wi-Fi, now marking one year of service, has emerged as... Read more
Amid increasing pressure on shipping to achieve the IMO 2050 decarbonisation targets, the Responsible... Read more
MacGregor continues to serve its maritime and offshore customers with its wide portfolio of cargo and... Read more
The board of directors of MacGregor Group AB has appointed Jonas Gustavsson Chief Executive Officer... Read more
Strategic lifting capacity meets India’s east coast logistics growth. The LHM 550s selected for... Read more
A new advanced simulation suite supplied by technology group Wärtsilä for the Akademi Laut... Read more
The New Nuclear for Maritime European Summit, the world’s largest international summit on maritime... Read more
Steelpaint GmbH has received its first order from Singapore-based Winning International Group to supply... Read more
Anemoi Marine Technologies, a leader in wind-assisted propulsion technology, has developed an in-service... Read more