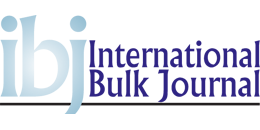

(Posted on 28/08/19)
A new secondary conveyor belt cleaner has been engineered specifically for challenging applications where traditional designs fail to deliver the necessary performance or wear life. The CleanScrape Secondary Cleaner (CS2) from Martin Engineering is particularly effective in conditions where continuous production is a high priority or cleaner service is difficult, including corrosive or high-temperature environments. Typically requiring just one re-tensioning during its lifespan, the extremely low maintenance requirements and outstanding cleaning ability help reduce cost of ownership in a wide range of industries, such as mining, coal processing, quarrying, cement production, scrap and other bulk material handling operations.
USA based Martin Engineering is a global innovator in the bulk material handling industry, developing new solutions to common problems and participating in industry organizations to improve safety and productivity.
An excellent solution for areas with restricted space, the unique all stainless steel design incorporates a matrix of specially-engineered carbide tips and is tensioned lightly to prevent damage to the belt or splices. Despite extremely low contact pressure between belt and cleaner, it has been shown to effectively remove potential carryback material that was not dislodged by a primary cleaner. The carbide cleaning surfaces deliver excellent performance, and the unit’s light touch helps protect against belt wear.
The CS2 can be used with any primary cleaner, but was engineered to be paired with the company’s original CleanScrape Primary Cleaner (CS1). When used together, they form a rugged, low-maintenance system that effectively removes carryback, helping to prevent fugitive material and the associated cleanup. The system represents a revolutionary concept that delivers superior cleaning and up to 4x the service life of conventional designs, with half the maintenance. The combination has been shown to remove as much as 99% of the carryback in most belt cleaning applications. The reduced service requirements and exceptional durability deliver a low life cycle cost, while allowing crews to focus on other tasks.
“Many carbide-tipped belt cleaners require high pressure against the belt in order to be effective, and they typically need to be re-tensioned often throughout their service life,” explained Chief Technology Officer Paul Harrison. “Like the CS1, this design is extremely effective with light tension against the belt, which helps avoid the damage to belts and slices that can occur with other carbide-tipped secondary cleaners. And because it only needs tensioning once during its lifespan, the maintenance requirements are very low.”
Harrison said that the negative rake angle of the CS2 is also key to the new design. “Some manufacturers use a positive angle of attack at the secondary position, which is greater than 90 degrees,” he continued. “That’s common in a urethane primary cleaner, which is tensioned tightly against the pulley. But using a ‘peeling’ action in a secondary cleaner can damage and prematurely wear the belt cover. It can be catastrophic on “beaver tails” (small sections of belt damage where a section of the top cover has separated from the belt carcass). With a negative rake angle and the ‘scraping’ action it provides, the CleanScrape Secondary Cleaner delivers outstanding performance, while mitigating potential belt damage.”
MacGregor continues to serve its maritime and offshore customers with its wide portfolio of cargo and... Read more
The board of directors of MacGregor Group AB has appointed Jonas Gustavsson Chief Executive Officer... Read more
Strategic lifting capacity meets India’s east coast logistics growth. The LHM 550s selected for... Read more
A new advanced simulation suite supplied by technology group Wärtsilä for the Akademi Laut... Read more
The New Nuclear for Maritime European Summit, the world’s largest international summit on maritime... Read more
Steelpaint GmbH has received its first order from Singapore-based Winning International Group to supply... Read more
Anemoi Marine Technologies, a leader in wind-assisted propulsion technology, has developed an in-service... Read more
A new recruitment feature has launched to help dismantle the shadow network of rogue crewing agents... Read more
AUMUND has announced that, as of 25 June, 2025, ESI Eurosilo B.V., headquartered in Purmerend, the Netherlands... Read more
Anemoi Marine Technologies, a global leader in wind propulsion solutions, has announced the official... Read more