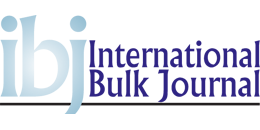

(Posted on 02/04/19)
Over the last few months the rudders and running gear of different types of vessels were given an Ecoshield protective coating at yards in the USA, Mexico, Canada, Turkey, Poland, Malta, Romania, China and Singapore.
Most of the ships treated belonged to different owners. Some of them were new customers, others returning ones. The returning customers had seen firsthand that Ecoshield solved the problem on their other rudders and wanted the same protection for the rest of their fleet. The new ones saw the excellent result obtained by other owners and chose Ecoshield to prevent corrosion and cavitation damage from reoccurring.
In the last couple of years Subsea Industries’ sister company Hydrex has noted a substantial increase in the number of enquiries for underwater rudder repairs. This clearly shows the need for a cost saving and lasting solution. A great deal of effort goes into the design and manufacture of rudders because they are such an important part of a vessel. If a rudder is not given the proper protection against cavitation and the resulting erosion and corrosion damage, the financial consequences can be substantial for the owner.
Before Ecoshield was launched the problem of cavitation damage to rudders and running gear remained unsolved. Cavitation caused erosion, pitting and sometimes complete failure, necessitating very expensive repairs or replacement. The need for repair to rudders, involving welding and resurfacing in drydock has been almost universal. Despite efforts to solve this problem, it has persisted.
Ecoshield puts an end to this. By removing the existing paint layers and applying the coating system on running gear the coating can break the never ending cycle of painting, suffering damage, having to perform extensive repairs in drydock followed by a full repainting, again and again. Ecoshield gives a very thorough and lasting defense for a ship’s entire service life. No repaint will be required during drydocking. At most minor touch-ups will be needed.
With time at a premium in drydock, the speed of application of Ecoshield is a further advantage. With the right planning grit blasting and application of the two required layers can be performed in just one day.
The coating prevents all cavitation or corrosion damage. As a result there is no need for a stainless steel belt to be installed in a nozzle or thruster tunnel when Ecoshield is applied. This saves precious money during the building process.
Maritime Information Services (MIS) has officially launched as a global media platform delivering daily... Read more
Russian and Ukrainian seafarers continue to experience significant psychological strain following the... Read more
Noatum Maritime, part of AD Ports Group’s Maritime & Shipping Cluster, announced the official... Read more
Leading vessel optimisation platform Smart Ship Hub has announced its partnership with AL Group &ndash... Read more
KR (Korean Register) has announced that LEE Jungkun, General Manager of KR’s Convention &... Read more
Dry bulk carriers entered with the International Association of Dry Cargo Shipowners (INTERCARGO) continue... Read more
The Nuclear Energy Maritime Organization (NEMO) is proud to announce that it has officially been granted... Read more
ICS, BIMCO, European Shipowners | ECSA, INTERCARGO and INTERTANKO have released a joint industry statement... Read more
NovaAlgoma Cement Carriers Limited, a joint venture between Algoma Central Corporation and Nova Marine... Read more
The Swedish Club has announced the appointment of Julia Ju as the new Chief Executive and Area Manager... Read more