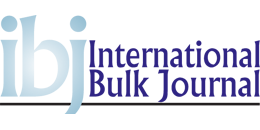

(Posted on 01/05/20)
In bulk material handling applications, a conveyor is typically a massive, complex and extremely powerful system. It’s usually constructed of rubber belting, set on rolling idlers, wrapped around large steel drums at each end and driven by a high-torque motor. As such, a conveyor presents enough danger zones that the entire system should be considered a hazard.
In most applications, a conveyor belt moves at a relatively constant speed, commonly running somewhere between 0.5 and 10 meters per second [≈100 to 2000 fpm]. An Olympic sprinter has a reaction time of about 0.18 seconds (roughly one-fifth of a second) when poised at the starting line and totally focused on the race. If this athlete becomes tangled in a conveyor belt traveling 1.5 meters per second [≈300 fpm], the person would be carried 0.27 meters [≈10.6 inches] before even realizing what has happened.
A ‘regular’ worker would likely require a longer time to react. For simplicity’s sake, we can assume it would be twice the athlete’s reaction time, so the worker would be pulled twice as far, introducing the potential to strike many more components or to be pulled farther and harder into the first one. In addition, most conveyors are engineered with the ability to start remotely. The system may go from dormant to active at any time at the push of a button, and that ability can suddenly catch a worker unaware, leading to serious injury or death.
“When a conveyor belt is moving, there will usually be more tension on the carrying side,” observed Martin Engineering Process Engineer Dan Marshall. “If the conveyor is merely stopped and de-energized, that tension may remain in the belt in the form of stored energy.”
Marshall reminded that a system under tension will always try to approach equilibrium; that is, it will try to release the energy. This release will likely come in the form of a pulley slip, which occurs when the belt slides around the head pulley to equalize the tension. The distance the belt will move is proportional to the amount of tension stored and the belt’s modulus (elasticity), possibly several feet. If a worker is on the belt or close enough to be pulled in during this sudden release of energy, injuries or death can occur.
“There’s a simple rule of thumb regarding conveyors: If it’s moving, don’t touch it,” Marshall continued. “The most common way to prevent inadvertent contact is with suitable guarding that renders the moving components inaccessible.” For maintenance or repairs, procedures for lockout/tagout/blockout/test-out should always be followed when working on a stationary conveyor, and systems should be equipped with anti-rollback devices (also known as backstops) on the head pulley.
Grupo Servicios Marítimos (GSM), in partnership with Neuero, has delivered a groundbreaking solution... Read more
Elcome International’s WELCOME Maritime Wi-Fi, now marking one year of service, has emerged as... Read more
Amid increasing pressure on shipping to achieve the IMO 2050 decarbonisation targets, the Responsible... Read more
MacGregor continues to serve its maritime and offshore customers with its wide portfolio of cargo and... Read more
The board of directors of MacGregor Group AB has appointed Jonas Gustavsson Chief Executive Officer... Read more
Strategic lifting capacity meets India’s east coast logistics growth. The LHM 550s selected for... Read more
A new advanced simulation suite supplied by technology group Wärtsilä for the Akademi Laut... Read more
The New Nuclear for Maritime European Summit, the world’s largest international summit on maritime... Read more
Steelpaint GmbH has received its first order from Singapore-based Winning International Group to supply... Read more
Anemoi Marine Technologies, a leader in wind-assisted propulsion technology, has developed an in-service... Read more