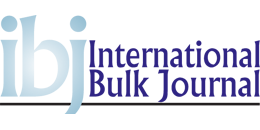

(Posted on 02/05/18)
The Cooperativa La Cruz Azul, the third-largest cement manufacturer in Mexico, required an entire packaging line for the flexible and fully automated filling, palletising and packaging of different types of a new tile mortar.
The BEUMER Group solution won out over the competition, providing everything from one single source. This included the BEUMER fillpac R filling system that was adapted for filling different materials. They also included the BEUMER bag placer to ensure a more efficient filling of the high-quality materials. With this new packaging line, Cruz Azul can achieve their projected production capacity.
Gigantic bridges, high-rises, tunnels for roads, subways and sewage systems: some of biggest construction projects in Latin America are currently being built in Mexico. This makes the country the second largest cement market on the continent, right after Brazil. In order to hold their own against national and international competition, Mexican manufacturers are developing more and more high-class materials. Cooperativa La Cruz Azul, headquartered in Mexico City, is one of them. The manufacturer operates four plants with a yearly production of around 8m tonnes of Portland cement per year, which is only one of its end products. The main plant is in Jasso in the state of Hidalgo. The city is located in a region that is very rich in limestone.
Its cement production represents 22 per cent of the national market. With the goal to further increase this share, the cooperative developed high-quality tile mortar in eight different variations as one of its new products. "The quality of the building materials is decisive in order to remain competitive," explained Victor Luna, Managing Director at Cruz Azul in Hidalgo. Distributors and end customers also want the products to arrive by the required date and quantity. A small amount of the mortar is sold in big bags, the majority however is sold in 20- and 25k bags. This is why the manufacturer needed an entire packaging line that could meet very specific requirements: due to varying material densities, and as a consequence different flow properties of the different variants of the new product line, the filling system had to be adjustable to the different materials as well as to smaller bag sizes without extensive retrofitting of the machine through the employees. The line should then palletise precise and stable bags stacks and package them to protect the content against transport damage and atmospheric influences.
"We have been working closely together for the last 30 years," said Victor Luna. "We have a long-standing relationship and trust in the BEUMER brand."
BEUMER Group presented the BEUMER fillpac R filling system to Cruz Azul. "Changing the required parameters is simple and quick and the different material is filled efficiently into two- to four-ply paper valve bags," explained Ralph Buchholz, Director General at BEUMER de México. Both companies quickly agreed on the scope and scheduling for the entire packaging line, and signed the contract already in April. "Cruz Azul attaches greatest value to the quality seal 'Made in Germany'," explained Buchholz. "Those responsible for the project even travelled to our headquarters in Beckum, Germany to accept the systems in person."
The BEUMER fillpac is equipped with an electronic calibration-capable weighing unit. It ensures that the bags are always filled with the same amount of material. A special software enables filling spouts and scale to constantly compare the weight. If the determined weight is incorrect, the bags are automatically removed, discharged on a chute and opened. The collected material is fed back into the process via a spillage screw conveyor and a bucket elevator.
The system has a modular structure. "We equipped the system with the new BEUMER bag placer because the material is so fine and volatile," said Buchholz. A ream magazine for 700 bags was also added. This allows Cruz Azul to further increase the efficiency of the filling system. Servomotors drive the application unit and the suction gripper automatically, precisely and energy-efficiently. The gripping system and the application unit apply the bag from the stack safely onto the filling spout. The system can pack 1,800 25-kg bags or 2,250 20-kg bags per hour with the highest precision. "The operator can also adjust the BEUMER bag placer to other bag formats," explains Buchholz.
The finished bag stacks are transported over roller conveyors to the BEUMER stretch hood packaging system. It packages 110 pallet stacks per hour with stretch film hoods with film thickness ranging from 40 to 100 micrometers. "It depends on the type of tile mortar," Buchholz explains. "The packaging protects the product against dust and humidity during storage and on long transport routes and ensures that the bags remain stable on the pallet without moving." In order to facilitate the work for the maintenance personnel and to ensure high system availability, the packaging system no longer needs a platform. Maintenance work, such as changing the blades or the sealing bars, is handled at floor level. Additional benefits include the compact design and the resulting low height and small footprint.
"The BEUMER stretch hood A is extremely energy efficient," emphasises Buchholz. A film transport system, which is particularly gentle on the material, introduces the previously cut and sealed film hood into the system. The sealing seam already cools down on the way to the crimping and stretching unit. Crimping can start without any delay. This allows for the elimination of energy-consuming cooling units and efficiency-reducing cooling times. This way the pallets can be packaged at a high bag sequencing.
MacGregor continues to serve its maritime and offshore customers with its wide portfolio of cargo and... Read more
The board of directors of MacGregor Group AB has appointed Jonas Gustavsson Chief Executive Officer... Read more
Strategic lifting capacity meets India’s east coast logistics growth. The LHM 550s selected for... Read more
A new advanced simulation suite supplied by technology group Wärtsilä for the Akademi Laut... Read more
The New Nuclear for Maritime European Summit, the world’s largest international summit on maritime... Read more
Steelpaint GmbH has received its first order from Singapore-based Winning International Group to supply... Read more
Anemoi Marine Technologies, a leader in wind-assisted propulsion technology, has developed an in-service... Read more
A new recruitment feature has launched to help dismantle the shadow network of rogue crewing agents... Read more
AUMUND has announced that, as of 25 June, 2025, ESI Eurosilo B.V., headquartered in Purmerend, the Netherlands... Read more
Anemoi Marine Technologies, a global leader in wind propulsion solutions, has announced the official... Read more