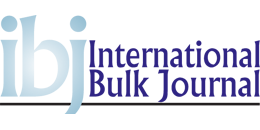

(Posted on 12/05/20)
Aalborg, Denmark, is the production site for Alfa Laval PureBallast 3 ballast water treatment systems. Having quickly adapted to the ongoing COVID-19 pandemic and lockdown measures from the Danish government, the factory continues to meet global production demands – and has even surpassed expectations.
“While the world has slowed down, the implementation of the ballast water management convention remains unchanged,” says Peter Sahlén, Head of Alfa Laval PureBallast. “We simply must continue meeting our customers’ needs, regardless of the obstacles.”
Considering that PureBallast 3 has a leading market position and many orders outstanding, those obstacles have been large indeed. The Aalborg facility normally bustles with manufacturing teams, customers, class society representatives and visitors. Nevertheless, Alfa Laval is securing customer deliveries, even with far fewer people on the factory floor.
Alfa Laval’s approach has been a combination of rapid response and innovative thinking. The company took swift action to implement protective measures for employees, but also to secure components and materials that would be needed in the coming months. When the Danish government imposed a strict lockdown on 11 March, the factory in Aalborg was well prepared.
“We moved quickly from two shifts to three shifts, working in smaller teams that can easily maintain a safe distance,” says Søren Nord Larsen, who manages the factory in Aalborg. “There’s no contact between shifts. So, if one of our workers should be infected, we can lift the entire shift out without impacting the others or any customer deliveries.”
Even meals and breaks are taken individually, at different times. Tools are carefully handled and disinfected regularly, and support functions like purchasing and production planning are managed digitally to the greatest extent possible.
“It’s tough to change so quickly and dramatically, but colleagues have really taken the situation with a positive attitude and adapted to the new routines,” says Larsen. “Many come with their own ideas for improving things, because everyone wants this to happen for our customers.”
The success of these efforts is undeniable, especially as Alfa Laval has managed to increase production during the same period. “We’ve proven that this can be done, and we’re not simply maintaining the status quo,” says Larsen. “In March we set a record of 400 systems produced for the quarter, and our deliveries for the quarter were yet another all-time high.”
For Peter Sahlén, the high productivity in Aalborg builds on Alfa Laval’s long-term planning. “We’ve made extensive preparations for ramp-up in the last two years, and that readiness has served us well in this unusual situation,” Sahlén says. “We already had a systematic overview and allocated resources, which made it easier to recalibrate. Together with our customers we will make it through this situation – and our production will be even stronger on the other side.”
Grupo Servicios Marítimos (GSM), in partnership with Neuero, has delivered a groundbreaking solution... Read more
Elcome International’s WELCOME Maritime Wi-Fi, now marking one year of service, has emerged as... Read more
Amid increasing pressure on shipping to achieve the IMO 2050 decarbonisation targets, the Responsible... Read more
MacGregor continues to serve its maritime and offshore customers with its wide portfolio of cargo and... Read more
The board of directors of MacGregor Group AB has appointed Jonas Gustavsson Chief Executive Officer... Read more
Strategic lifting capacity meets India’s east coast logistics growth. The LHM 550s selected for... Read more
A new advanced simulation suite supplied by technology group Wärtsilä for the Akademi Laut... Read more
The New Nuclear for Maritime European Summit, the world’s largest international summit on maritime... Read more
Steelpaint GmbH has received its first order from Singapore-based Winning International Group to supply... Read more
Anemoi Marine Technologies, a leader in wind-assisted propulsion technology, has developed an in-service... Read more