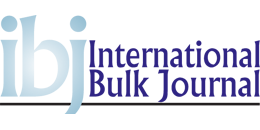

(Posted on 11/04/23)
When a fully laden, 300 x 50m, 207,000 ton DWT bulk carrier suffered heavy damages from a grounding in Suez, the owners and management’s first thought was to call Hydrex. Over the years, Hydrex has earned a reputation for being able to tackle the most challenging underwater and afloat rescue and repair operations. In this case the ship was carrying a valuable cargo and every day she was out of action represented a huge loss to the owners.
Hydrex was contacted by the vessel’s management requesting urgent assistance with repairing the damage so that the ship could sail again. The ship had suffered a breach of the hull and port side water ballast tanks (WBT) 1, 2 and 3 were letting in water. The ship was moved under state and class supervision and with a tug escort to Great Bitter Lake for an underwater survey. When the call for help arrived at Hydrex headquarters in Antwerp, the Hydrex team responded immediately. Calls of this nature are answered 24/7. There is always someone on duty to take the call and start the necessary actions to begin the job.
Hydrex proposed sending a team of divers to the ship in Suez to assess the damage and gather the information needed to come up with a detailed plan for repairs to enable the ship to sail to drydock. This proposal was accepted and the team rapidly mobilized.
The underwater inspection revealed and documented the full extent of the damage, which was quite severe. It included one hull penetration at the turn of bilge 7m long with a maximum width of 5m and another smaller penetration of 10x5 cm.
Based on the initial inspection and rough measurements, a plan was proposed to carry out precise measurements of the hull where the large damage occurred so that a cofferdam could be designed which would then be installed to make the hull watertight so that the water ballast tanks could be pumped out.
The proposal for handling the additional damage was to arrest the crack by drilling holes and then weld a doubler plate over the large crack in the hull. The plan was approved by class (LR), and ship management gave the go ahead to implement it. The Hydrex team took full measurements of the hull in the damaged area using a fabricated frame. The measurements were relayed to the engineers in Antwerp who produced drawings for the yard in Egypt where the cofferdam was fabricated. The final cofferdam consisted of a frame or shell with a flange built to the shape of the hull and insulation material to make it watertight.
As soon as the fabrication was completed, a Hydrex team of eight diver/welder/technicians flew back to Suez to install the cofferdam. After some needed modification, the massive, 45-ton cofferdam was lowered into position by crane and secured against the hull with welded screw dogs, stoppers and thick seals.
However, with the cofferdam secured in place, when an attempt was made to empty out WBT 2, the pressure of the water was too much for the structurally weak hull which started to cave in under the force. Evacuation of the ballast tank was halted. It became clear that the ship had suffered too much internal damage to permit the water ballast tanks to be fully pumped out. This was not something that could have been predicted or remedied with the ship afloat.
In order to reinforce the bulkhead between the water ballast tanks, a new plan was proposed to build cement boxes and pour concrete to provide enough strength for the bulkheads in between the ballast tanks. But WBT 2 port could not be emptied. Part of the plan, therefore, was to lighter the ship as necessary until the class-required draft could be achieved.
With the cement boxes in place, the cofferdam was fully secured and sea trials were conducted. The officers and crew of the ship were very happy with the results and a final inspection of the cofferdam was conducted and showed that all was secure and ready for sailing. The Hydrex team’s job was done and they headed home to Antwerp. Many of them had spent their Christmas working on the distressed vessel. It was a long haul with many ups and downs and unexpected twists and turns, but in the end, persistence won the day.
Because WBT 2 could not be pumped out, the ship had to be partially lightered so that the class-required draft could be achieved and she could sail on to drydock. Once the ship was dry, it was possible to see the sheer magnitude of the repair job. It was the largest cofferdam ever installed in a hull repair by Hydrex. It remained firmly in place until it could be removed when the ship was in drydock and permanent hull repair could be carried out.
Grupo Servicios Marítimos (GSM), in partnership with Neuero, has delivered a groundbreaking solution... Read more
Elcome International’s WELCOME Maritime Wi-Fi, now marking one year of service, has emerged as... Read more
Amid increasing pressure on shipping to achieve the IMO 2050 decarbonisation targets, the Responsible... Read more
MacGregor continues to serve its maritime and offshore customers with its wide portfolio of cargo and... Read more
The board of directors of MacGregor Group AB has appointed Jonas Gustavsson Chief Executive Officer... Read more
Strategic lifting capacity meets India’s east coast logistics growth. The LHM 550s selected for... Read more
A new advanced simulation suite supplied by technology group Wärtsilä for the Akademi Laut... Read more
The New Nuclear for Maritime European Summit, the world’s largest international summit on maritime... Read more
Steelpaint GmbH has received its first order from Singapore-based Winning International Group to supply... Read more
Anemoi Marine Technologies, a leader in wind-assisted propulsion technology, has developed an in-service... Read more